We offer more than 75 crushed stone products available in a variety of colors, sizes, and gradations.
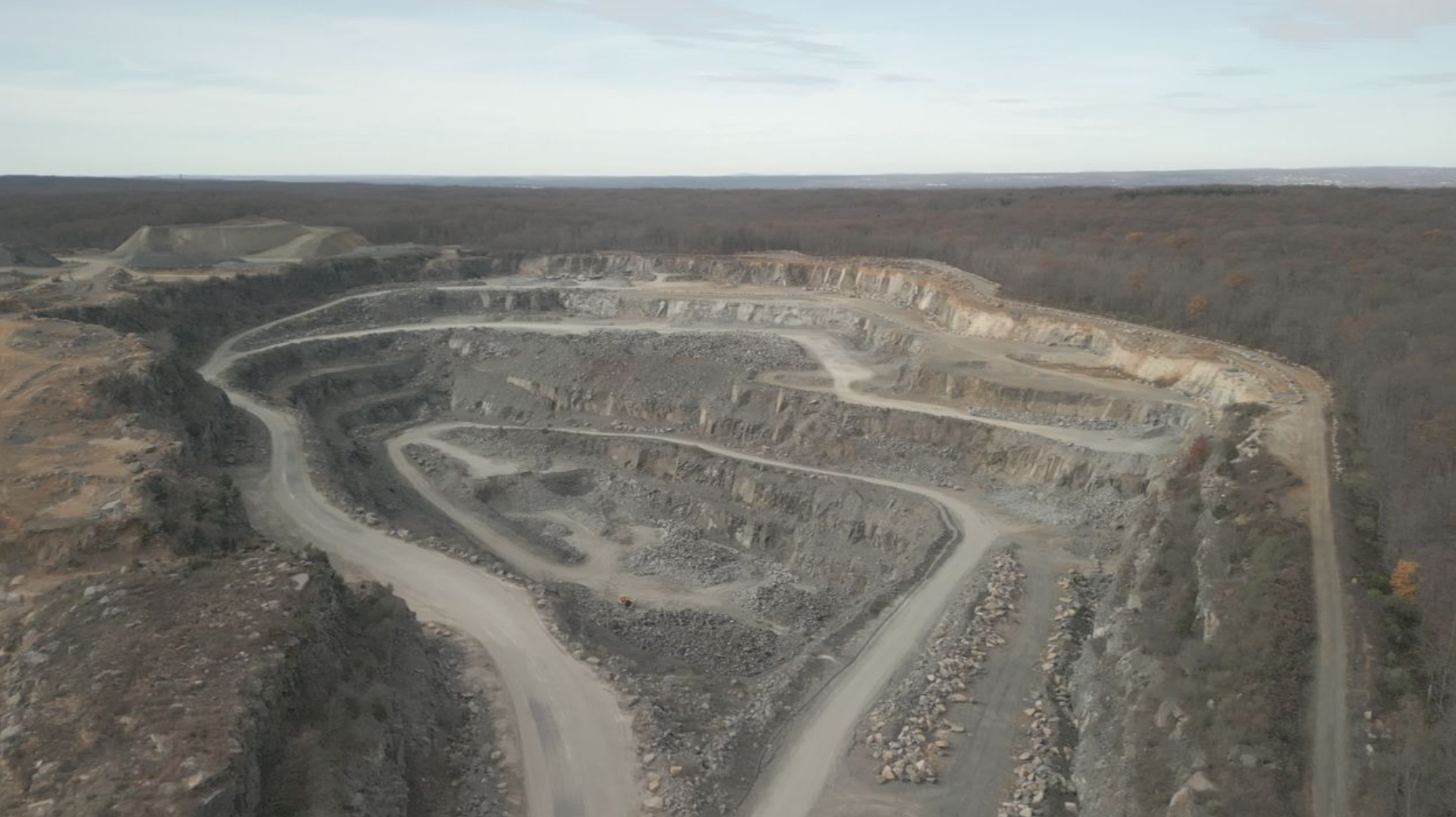
How Stone and Aggregate Delivery Costs Affect Construction Budgets
In the construction industry, managing stone and aggregate delivery costs is essential for staying on budget — and one of the biggest cost drivers is transportation. The cost of delivering stone and aggregate materials can significantly impact the overall budget of a project, especially for large-scale jobs. Understanding the factors behind delivery costs — and how strategic sourcing from suppliers can reduce those costs — is key to improving efficiency and profitability.
Why Delivery Costs Matter in Construction
Stone and aggregate materials are essential for building strong foundations, roadbeds, and infrastructure. While the cost of the material itself matters, transportation costs can sometimes exceed the material cost — particularly when dealing with long-distance hauling or challenging logistics. Several factors influence stone delivery costs:
- Distance from the Quarry – The farther the materials need to travel, the higher the transportation costs due to fuel, labor, and vehicle wear.
- Hauling and Back-Hauling Costs – Delivering stone requires large, heavy-duty trucks, which are expensive to operate. Back-hauling (returning with an empty truck) increases costs further.
- Fuel Prices and Tolls – Fluctuations in fuel prices and toll charges on major highways can add to delivery expenses.
- Weight and Load Size – Hauling heavier loads increases fuel consumption and puts more strain on vehicles, raising operating costs.
- Traffic and Road Conditions – Congested routes, road construction, and seasonal weather conditions can increase delivery times and costs.
Truck vs. Rail Delivery Costs: Which Is More Efficient?
Delivery costs vary depending on whether materials are transported by truck or rail. Here’s how they compare:
- Cost Per Ton: Truck delivery tends to be more expensive due to fuel and labor costs, while rail delivery is more cost-effective for large orders.
- Lead Time: Truck delivery is faster for short distances, but rail is more efficient for long hauls.
- Capacity: Trucks are limited by size and weight, while rail can handle larger volumes.
- Environmental Impact: Truck delivery has a higher carbon footprint; rail delivery is more fuel-efficient and environmentally friendly.
By understanding these factors, contractors can make more informed decisions about sourcing and delivery methods — ultimately improving project efficiency and controlling costs.
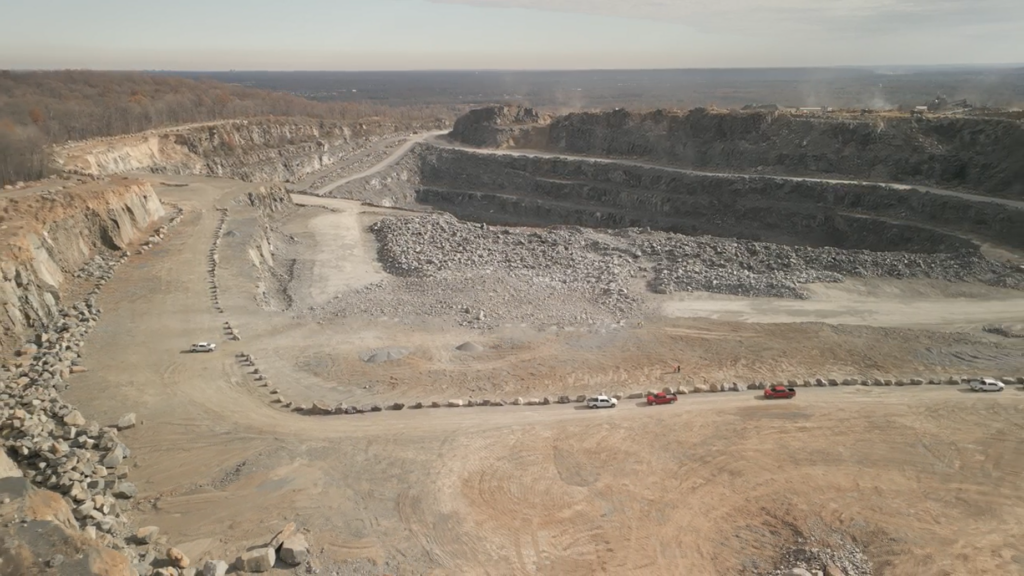
How Back-Hauling Affects Costs
A major challenge in stone delivery is back-hauling — when a truck returns to the quarry empty after delivering materials. This doubles the fuel and labor costs without generating additional revenue. Suppliers can reduce back-hauling costs by:
- Coordinating return loads whenever possible.
- Working with local partners to fill return trips.
- Optimizing delivery schedules to reduce empty truck miles.
Reducing back-hauling costs allows suppliers to offer more competitive pricing and improve delivery efficiency.
How Contractors Can Save on Stone Delivery Costs
While delivery costs are a reality of the construction industry, contractors can take steps to manage these expenses:
- Source Locally When Possible – Partnering with suppliers near the job site reduces hauling distance and costs.
- Leverage Rail Transport for Large Jobs – Rail delivery is more cost-effective for large projects requiring high volumes of material.
- Bundle Orders to Reduce Trips – Ordering stone, sand, and cement from a single supplier like Silvi Materials reduces the number of trips needed.
- Plan Deliveries During Off-Peak Hours – Avoiding traffic and road congestion can cut down on delivery time and fuel use.
Why Silvi Materials is a Smart Choice for Large-Scale Stone Projects
Silvi Materials’ ability to deliver a wide range of construction materials — including stone, sand, and cement — gives contractors a unique advantage. By consolidating orders through one supplier, contractors can reduce delivery complexity, lower costs, and improve project efficiency.
Silvi Stone of Belle Mead is strategically positioned near major transportation routes — including I-76, I-95, and the New Jersey Turnpike — which allows for faster and more efficient delivery to job sites. In addition to Belle Mead, Silvi Materials also operates Silvi Stone of New Hanover in Perkiomenville, PA, expanding delivery capacity and improving coverage for contractors across the region.
Silvi Materials also has a rail spur at its Belle Mead quarry — a key advantage over competitors. Transporting stone by rail instead of truck can significantly lower costs for large-scale projects, particularly when servicing markets like New York City, Philadelphia, and northern New Jersey.
Advantages of Rail Access:
- Reduced fuel consumption per ton of material.
- Lower labor costs compared to long-distance trucking.
- More reliable delivery schedules.
In addition to strategic rail and truck delivery options, Silvi Stone’s expert team works with contractors to create delivery plans that minimize costs and maximize productivity.
“Silvi Materials’ logistical expertise and ability to deliver multiple materials to a single site allow contractors to save time and increase efficiency on important projects.”
The Bottom Line on Stone Delivery Costs
Managing stone and aggregate delivery costs is essential for maintaining construction budgets. By understanding the factors driving transportation expenses and choosing a supplier with flexible delivery options, contractors can reduce costs and improve project efficiency.