We offer more than 75 crushed stone products available in a variety of colors, sizes, and gradations.

How Cement Is Made: From Quarry to Kiln to Silo
Cement is the backbone of modern infrastructure — from bridges and highways to residential slabs and precast panels. But while builders, engineers, and contractors rely on cement every day, even industry insiders don’t always get a clear view of how it’s actually made.
This behind-the-scenes look demystifies the manufacturing process of portland cement, from raw materials to terminal storage. Whether you’re an experienced contractor or just brushing up on the fundamentals, understanding the cement production process can help you make smarter sourcing and mix design decisions.
Quarrying the Raw Materials
The cement-making process begins with limestone — a sedimentary rock rich in calcium carbonate. Quarry operations extract massive quantities of limestone, which is the primary ingredient in portland cement. Other essential raw materials include shale, clay, sand, and iron ore.
These materials are carefully blended to create a consistent feedstock for the kiln. The goal is to produce the right balance of calcium, silica, alumina, and iron — which will ultimately dictate the performance of the finished product.
Crushing and Raw Material Preparation
Once extracted, the raw materials are crushed into smaller particles using heavy-duty crushers. This reduces the rock to a manageable size before it’s blended and ground into a fine powder known as raw meal.
This blend is carefully monitored to ensure it meets chemical composition targets. Even slight deviations can impact how the cement reacts with water or how it performs in the field.
Preheating and Pyroprocessing in the Kiln
The raw meal enters a preheater tower, where it’s gradually heated using hot gases from the kiln. This process drives off moisture and begins to chemically alter the material. From there, the material enters the rotary kiln — a massive, rotating steel tube that reaches temperatures up to 1,450°C (2,642°F).
Inside the kiln, raw materials undergo a chemical transformation called calcination. Limestone (CaCO₃) breaks down into calcium oxide (CaO), releasing carbon dioxide (CO₂). Silica, alumina, and iron compounds react with the CaO to form clinker — hard, nodular material that looks like gray marbles.
Clinker is the essential component of cement and contains all the properties needed for hydration and strength development.
Cooling and Final Grinding
The hot clinker exits the kiln and moves into a clinker cooler, where air is forced through the material to rapidly cool it. This is essential to preserve the mineral structure and prepare the material for grinding.
Once cooled, the clinker is mixed with a small amount of gypsum and ground into a fine powder — portland cement. The grinding process ensures that the particles are small and uniform, which is critical for workability, hydration, and strength development in concrete.
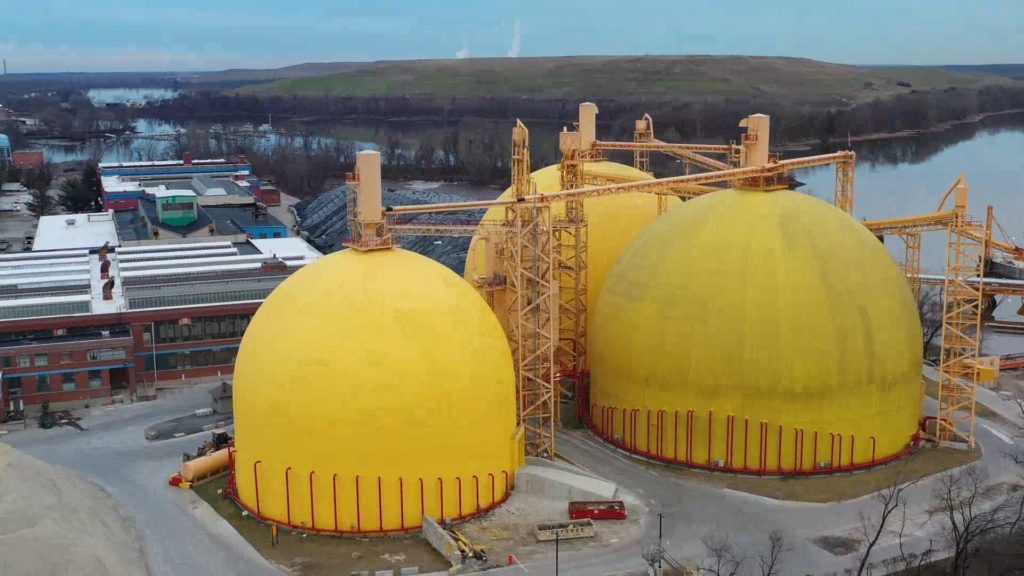
Transport and Terminal Storage
In many regions, cement is imported rather than manufactured locally. Once produced and cooled, the finished product is shipped in bulk — often by vessel — to marine terminals for storage and regional distribution. At these terminals, the product is unloaded and stored in dedicated silos to protect quality and ensure consistent supply.
From terminal storage, cement is distributed to end users via multiple transportation modes. Tanker trucks are commonly used for local and regional deliveries, while rail transport offers a cost-effective option for reaching inland markets or high-volume destinations. Terminals equipped with rail spurs and pneumatic loading systems support this intermodal approach, helping to meet demand efficiently across a wide service area.
A Closer Look at Cement Types
While ordinary portland cement (OPC) is the most widely used, cement can be blended with other materials to enhance performance and sustainability. One common blend is with ground granulated blast-furnace slag (GGBFS), known as slag cement — a supplementary cementitious material that improves long-term strength and reduces permeability.
Why Understanding the Cement Process Matters
Understanding how cement is produced gives construction professionals a better appreciation for how raw materials, processing methods, and storage conditions affect quality. Here’s how that knowledge translates into smarter decisions on the job:
- Material Consistency: Knowing that cement starts with quarry-controlled materials and undergoes multiple quality control checks reinforces the importance of consistent sourcing.
- Mix Performance: Understanding clinker formation and grinding helps explain how cement strength and setting behavior can vary by type or supplier.
- Sustainability: Learning about calcination and CO₂ release can help contractors and engineers make informed choices about supplementary cementitious materials (SCMs) like slag, which reduce cement content and emissions.
- Logistics Efficiency: Familiarity with terminal-based delivery (rather than plant-direct manufacturing) helps project managers and buyers better plan lead times and reduce costly delays.
From quarry to kiln to silo, the cement used in today’s construction projects is the product of carefully engineered processes, rigorous quality control, and strategic logistics. Understanding this journey helps contractors, engineers, and builders make informed decisions — whether evaluating material performance, planning delivery timelines, or selecting supplementary cementitious materials for sustainability.
No matter the application, high-quality cement remains essential to durable, efficient, and high-performing concrete construction.